Aluminum - (Al)
Melting
Point:
1221
Fahrenheit
\ 660
Celsius
Boiling
Point:
4566
Fahrenheit
\ 2519
Celsius
Note:
Aluminium versus Aluminum,
see below.
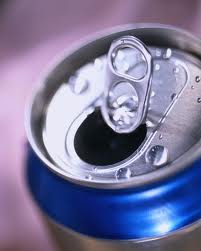
Aluminum
is a soft,
durable,
lightweight,
ductile
and
malleable
metal with
appearance
ranging
from
silvery to
dull gray,
depending
on the
surface
roughness.
Aluminum
is
nonmagnetic
and has
about
one-third
the
density
and
stiffness
of steel
and
resists
corrosion
due to the
phenomenon
of
passivation.
It is
easily
machined,
cast,
drawn and
extruded.
Aluminum,
unlike
steel,
melts
without
first
glowing
red which
gives no
visual
signs to
reveal how
close the
material
is to
melting.
Aluminum
Does Not
Emit
Sparks.
Because
aluminum
is
non-sparking,
it is
appropriate
for
applications
involving
explosive
materials
or taking
place in
highly
flammable
environments.
Aluminum
is the
most
widely
used
non-ferrous
metal
exceeding
other
metals
except
iron.
Aluminum
is a good
thermal
and
electrical
conductor,
having 59%
the
conductivity
of copper,
both
thermal
and
electrical.
Corrosion
resistance
can be
excellent
due to a
thin
surface
layer of
aluminum
oxide that
forms when
the metal
is exposed
to air,
effectively
preventing
further
oxidation.
The
strongest
aluminum
alloys are
less
corrosion
resistant
due to
galvanic
reactions
with
alloyed
copper.
This
corrosion
resistance
is also
often
greatly
reduced
when many
aqueous
salts are
present,
particularly
in the
presence
of
dissimilar
metals.
Aluminum
is
theoretically
100%
recyclable
without
any loss
of its
natural
qualities.
Recycling
involves
melting
the scrap,
a process
that
requires
only 5% of
the energy
used to
produce
aluminum
from ore,
though a
significant
part (up
to 15% of
the input
material)
is lost as
dross
(ash-like
oxide).
The dross
can
undergo a
further
process to
extract
aluminum.
Recycling
Aluminum
saves raw
materials
such as
carbon and
alumina.
Another
advantage
is that
waste
product
can be
recycled
instead of
being sent
to
landfill.
Recycled
aluminum
is known
as
secondary
aluminum,
but
maintains
the same
physical
properties
as primary
aluminum.
Secondary
aluminum
is
produced
in a wide
range of
formats
and is
employed
in 80% of
alloy
injections.
Another
important
use is for
extrusion.
Beverage
Can
The most
common
daily used
Aluminum
product is
the
beverage
can which
is of
incredibly
thin yet
strong
design. An
empty
aluminum
can weighs
approximately
half an
ounce (15
g). There
are
roughly 30
empty
aluminum
cans to a
pound or
70 to a
kilogram.
Alloy
Aluminum
6061 is
used in
the
manufacture
of
aluminum
cans for
the
packaging
of
foodstuffs
and
beverages.
ALLOY:
Aluminum
is almost
always
alloyed,
which
markedly
improves
its
mechanical
properties,
especially
when
tempered.
For
example,
the common
aluminum
foils and
beverage
cans are
alloys of
92% to 99%
aluminum.
The main
alloying
agents are
copper,
zinc,
magnesium,
manganese,
and
silicon
(e.g.,
duralumin)
and the
levels of
these
other
metals are
in the
range of a
few
percent by
weight.
Aluminum
alloys
with a
wide range
of
properties
are used
in
engineering
structures.
Alloy
systems
are
classified
by a
number
system
(ANSI) or
by names
indicating
their main
alloying
constituents
(DIN and
ISO).
Aluminum
(Alloy
1100)
This grade
is
commercially
pure
aluminum.
It is soft
and
ductile
and has
excellent
workability.
It is
ideal for
applications
involving
intricate
forming
because it
work
hardens
more
slowly
than other
alloys. It
is the
most
weldable
of
aluminum
alloys, by
any
method. It
is non
heat-treatable.
It has
excellent
resistance
to
corrosion
and is
widely
used in
the
chemical
and food
processing
industries.
It
responds
well to
decorative
finishes
which make
it
suitable
for
giftware.
Aluminum
(Alloy
2011)
This is
the most
free-machining
of the
common
aluminum
alloys. It
also has
excellent
mechanical
properties.
Thus, it
is widely
used for
automatic
screw
machine
products
in parts
requiring
extensive
machining.
Aluminum
(Alloy
2014 &
2017)
The 2017
alloy
combines
excellent
machinability
and high
strength
with the
result
that it is
one of the
most
widely
used
alloys for
automatic
screw
machine
work. It
is a
tough,
ductile
alloy
suitable
for
heavy-duty
structural
parts. Its
strength
is
slightly
less than
that of
2014.
Aluminum
(Alloy
2024)
This is
one of the
best known
of the
high
strength
aluminum
alloys.
With its
high
strength
and
excellent
fatigue
resistance,
it is used
to
advantage
on
structures
and parts
where good
strength-to-weight
ratio is
desired.
It is
readily
machined
to a high
finish. It
is readily
formed in
the
annealed
condition
and may be
subsequently
heat
treated.
Arc or gas
welding is
generally
not
recommended,
although
this alloy
may be
spot, seam
or flash
welded.
Since
corrosion
resistance
is
relatively
low, 2024
is
commonly
used with
an
anodized
finish or
in clad
form (“Alclad”)
with a
thin
surface
layer of
high
purity
aluminum.
Applications:
aircraft
structural
components,
aircraft
fittings,
hardware,
truck
wheels and
parts for
the
transportation
industry.
Aluminum
(Alloy
3003)
This is
the most
widely
used of
all
aluminum
alloys. It
is
essentially
commercially
pure
aluminum
with the
addition
of
manganese
which
increases
the
strength
some 20%
over the
1100
grade.
Thus, it
has all
the
excellent
characteristics
of 1100
with
higher
strength.
It has
excellent
corrosion
resistance.
It has
excellent
workability
and it may
be deep
drawn or
spun,
welded or
brazed. It
is non
heat
treatable.
Applications:
cooking
utensils,
decorative
trim,
awnings,
siding,
storage
tanks,
chemical
equipment.
Aluminum
(Alloy
5005)
This alloy
is
generally
considered
to be an
improved
version of
3003. It
has the
same
general
mechanical
properties
as 3003
but
appears to
stand up
better in
actual
service.
It is
readily
workable.
It can be
deep drawn
or spun,
welded or
brazed. It
has
excellent
corrosion
resistance.
It is non
heat-treatable.
It is well
suited for
anodizing
and has
less
tendency
to streak
or
discolor.
Applications
same as
3003.
Aluminum
(Alloy
5052)
This is
the
highest
strength
alloy of
the more
common non
heat-treatable
grades.
Fatigue
strength
is higher
than most
aluminum
alloys.In
addition
this grade
has
particularly
good
resistance
to marine
atmosphere
and salt
water
corrosion.
It has
excellent
workability.
It may be
drawn or
formed
into
intricate
shapes and
its
slightly
greater
strength
in the
annealed
condition
minimizes
tearing
that
occurs in
1100 and
3003.
Applications:
Used in a
wide
variety of
applications
from
aircraft
components
to home
appliances,
marine and
transportation
industry
parts,
heavy duty
cooking
utensils
and
equipment
for bulk
processing
of food.
Aluminum
(Alloy
5083 &
5086)
For many
years
there has
been a
need for
aluminum
sheet and
plate
alloys
that would
offer, for
high
strength
welded
applications,
several
distinct
benefits
over such
alloys as
5052 and
6061. Some
of the
benefits
fabricators
have been
seeking
are
greater
design
efficiency,
better
welding
characteristics,
good
forming
properties,
excellent
resistance
to
corrosion
and the
same
economy as
in other
non
heat-treatable
alloys.
Metallurgical
research
has
developed
5083 and
5086 as
superior
weldable
alloys
which fill
these
needs.
Both
alloys
have
virtually
the same
characteristics
with 5083
having
slightly
higher
mechanical
properties
due to the
increased
manganese
content
over 5086.
Applications:
unfired
pressure
vessels,
missile
containers,
heavy-duty
truck and
trailer
assemblies,
boat hulls
and
superstructures.
Aluminum
(Alloy
6061)
This is
the least
expensive
and most
versatile
of the
heat-treatable
aluminum
alloys. It
has most
of the
good
qualities
of
aluminum.
It offers
a range of
good
mechanical
properties
and good
corrosion
resistance.
It can be
fabricated
by most of
the
commonly
used
techniques.
In the
annealed
condition
it has
good
workability.
In the T4
condition
fairly
severe
forming
operations
may be
accomplished.
The full
T6
properties
may be
obtained
by
artificial
aging. It
is welded
by all
methods
and can be
furnace
brazed. It
is
available
in the
clad form
(“Alclad”)
with a
thin
surface
layer of
high
purity
aluminum
to improve
both
appearance
and
corrosion
resistance.
Applications:
This grade
is used
for a wide
variety of
products
and
applications
from truck
bodies and
frames to
screw
machine
parts and
structural
components.
6061 is
used where
appearance
and better
corrosion
resistance
with good
strength
are
required.
Aluminum
(Alloy
6063)
This grade
is
commonly
referred
to as the
architectural
alloy. It
was
developed
as an
extrusion
alloy with
relatively
high
tensile
properties,
excellent
finishing
characteristics
and a high
degree of
resistance
to
corrosion.
This alloy
is most
often
found in
various
interior
and
exterior
architectural
applications,
such as
windows,
doors,
store
fronts and
assorted
trim
items. It
is the
alloy best
suited for
anodizing
applications
- either
plain or
in a
variety of
colors.
Aluminum
(Alloy
7075)
This is
one of the
highest
strength
aluminum
alloys
available.
Its
strength-to
weight
ratio is
excellent
and it is
ideally
used for
highly
stressed
parts. It
may be
formed in
the
annealed
condition
and
subsequently
heat
treated.
Spot or
flash
welding
can be
used,
although
arc and
gas
welding
are not
recommended.
It is
available
in the
clad (“Alclad”)
form to
improve
the
corrosion
resistance
with the
over-all
high
strength
being only
moderately
affected.
Applications:
Used where
highest
strength
is needed.
Precision-Cast
Multipurpose
Aluminum
(MIC 6
Alloy)
For
outstanding
machinability
and
stability,
turn to
this
stress-relieved
cast
alloy.
Mold-Quality
Aluminum
(QC-10
Alloy)
Outstanding
thermal
conductivity,
when
compared
to steel,
along with
high
strength
and
surface
hardness
make this
heat-treatable
alloy
suitable
for use in
production
injection
molds and
blow
molds.
Porous
Mold-Quality
Aluminum
Perfect
for
creating
molds used
in vacuum
forming
and
thermoforming,
this
aluminum
alloy is
porous to
let air
and
moisture
through,
preventing
bubbles
and
blemishes
in your
material
when
forming.
Aluminum
Casting
When
products
aren't
made by
other raw
alloy
stock
machining
processes
the most
common
method is
by
casting.
Aluminum
melts at a
relatively
low
temperature
and can be
poured
into an
infinate
variety of
shapes for
many
purposes.
Cookware,
motor
parts and
lawn
furniture
to name a
few give
examples
of casting
aluminum.
One of the
main
advantages
to using
cast
aluminum
is that
the metal
is often
cost
efficient
in
comparison
to other
cast
metals.
Along with
the lower
cost, the
metal also
retains a
high
degree of
durability.
While it
is not
necessarily
true that
cast
aluminum
will last
as long as
cast iron
in some
applications,
the
aluminum
products
do tend to
hold up
well for a
number of
years. The
combination
of lower
cost and
reliable
durability
makes cast
aluminum
an
excellent
choice for
a number
of metal
components
and
products
in
domestic
and
commercial
applications.
Health
concerns
In very
high
doses,
aluminum
can cause
neurotoxicity,
and is
associated
with
altered
function
of the
blood-brain
barrier. A
small
percentage
of people
are
allergic
to
aluminum
and
experience
contact
dermatitis,
digestive
disorders,
vomiting
or other
symptoms
upon
contact or
ingestion
of
products
containing
aluminum,
such as
deodorants
or
antacids.
In those
without
allergies,
aluminum
is not as
toxic as
heavy
metals,
but there
is
evidence
of some
toxicity
if it is
consumed
in
excessive
amounts.
Also see:
http://www.osha.gov/SLTC/metalsheavy/aluminum.html
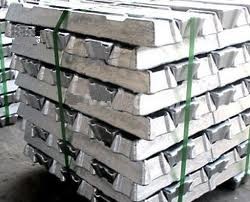
Aluminum
is the
third most
abundant
element
(after
oxygen and
silicon),
and the
most
abundant
metal, in
the
Earth's
crust. It
makes up
about 8%
by weight
of the
Earth's
solid
surface.
As
Aluminum
is mostly
alloyed
with other
metals the
raw ingot
source
selection
and prices
vary
greatly.
In small
user
quantities
expect to
pay 3.00
to 6.00 a
pound.
About Metal Spot Prices: The spot price of metals is based on paper contracts for delivery of tons of pure metal ingots. When you're not prepared to pay for and take delivery of tons of metal, that spot price will quickly become a huge understatement of the real price of that metal. When you want to buy just a few pounds of aluminum for example, you're looking at substantially higher prices, 2x, 3x, 4x, 5x more. Moreover, once you own physical aluminum ingots from your efforts, make absolutely sure you never sell for the spot price of aluminum. That's because it's hard to get investment / ingot grade aluminum or any metal in physical form without paying for it, so you've got something special on your hands and make sure to extract the full value when you're selling and understand the reverse when buying!
**
Aluminium
versus
Aluminum?
Globally
and on the
periodic
table the
element
(Al) is
spelled
Aluminium,
however in
North
America
(USA /
Canada) it
is common
to spell
it as
Aluminum,
USA from –ium
to –um. It
has to do
with Sir
Humphry
Davy, the
British
chemist
who
discovered
the metal
in 1808
and then
named it “alumium"
with one “i”
and an “ium”
ending.
Later in
his book
Elements
of
Chemical
Philosophy,
published
in 1812
Davy
changed
his mind
and gave
the metal
the name
“aluminum”
Other
scientists
at the
time
schooled
in fomal
scientific
latin word
origins
began
calling it
“aluminium”instead
believing
the “ium”
ending was
more
consistent
with other
elements
even
though
other
elements
like
molybdenum,
tantalum,
platinum,
and
lanthanum
exist.
From that
time both
“aluminum”
and “aluminium”
could be
found in
the US as
well as in
Britain.
Eventually
“aluminum”
became the
standard
name for
the metal
in North
America
and was
officially
adopted in
the 1920s
by the
American
Chemical
Society.
Elsewhere,
though,
scientists
generally
use “aluminium.”
The
International
Union of
Pure and
Applied
Chemistry
uses “aluminium”
as the
standard
international
spelling
but also
recognizes
“aluminum”
as a
variant.